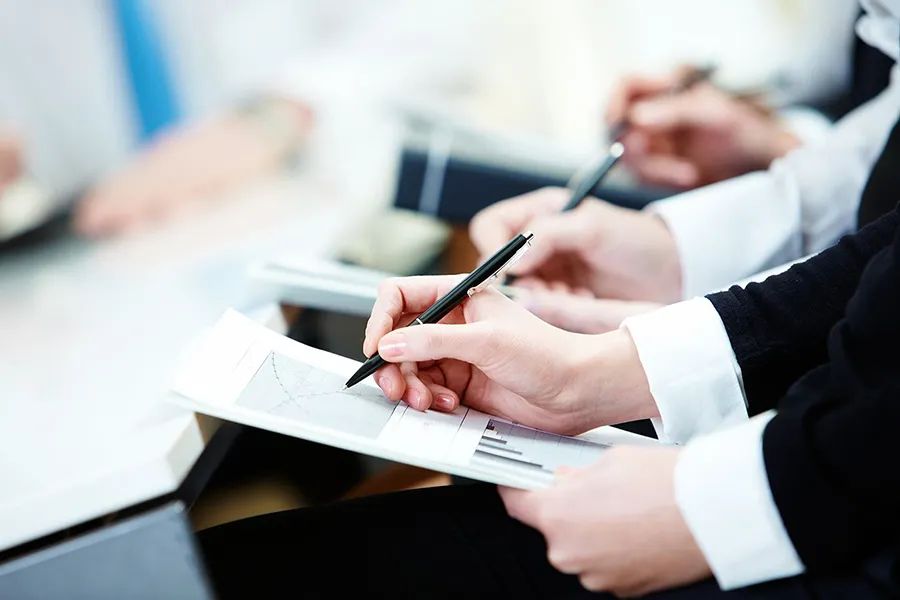
品質事故をなくすための
品質事故・クレームゼロへのアプローチ
~最先端テクノロジーを駆使した検査体制と品質保証体制の構築~
~不良ゼロを実現し、コストダウンしながらクレームゼロを実現~
~設計ミスゼロ、部材不良ゼロ、海外工場の品質向上の実現~
クレームの実態と5つの原因と17の施策,不良をゼロにする不良の71の要因と54の対策,設計ミスゼロ,
部材不良ゼロ,海外工場品質向上について品質事故の芽を摘み取るために解説する特別セミナー!!
- 講師
株式会社 ロンド・アプリウェアサービス 代表取締役社長 中崎 勝 先生
ブリヂストン,日本DECを経て現職
- 日時
- 会場
- 受講料
- (消費税等込み)1名:48,600円 同一セミナー同一企業同時複数人数申込みの場合 1名:43,200円
- テキスト
受講概要
受講対象 製造業の品質保証部門、生産部位の責任者、管理・監督者、リーダー、スタッフ 予備知識 特にありません 習得知識 1)品質事故、クレームの防止策、不良をゼロにする基礎知識 2)設計ミスをゼロにする基礎知識、部材不良をゼロにする基礎知識 3)海外工場の品質を向上させる基本的な考え方 講師の言葉 講師は、2000年当時から「品質事故」という異常な現象に注目し、その原因を追究し対策を立案し、 「今、日本の品質があぶない」というテーマで講演をし続けてきました。 本セミナーでは、品質事故(クレーム)の実態と5つの原因と17の施策を解説します。 17の施策の中には、不良を絶対に外に出さないためのAIの自動検査を使った検査のしくみ、品質データを 介在できない報告書を音声で入力するしくみなど最先端テクノロジーを使ったしくみも使っています。 また、コストダウンしながらクレームゼロを実現する健全なクレーム対策として不良をゼロにする具体的な アプローチも紹介します。 不良ゼロへのアプローチでは、不良の71の要因と54の対策を紹介し、誰でも簡単に不良をゼロに できる方法を提供します。 今、日本の企業ではどこが品質事故を起こしても不思議ではない状態に陥っています。 みなさんが知らないうちにその芽は発芽しているかもしれません。 危機的状況に陥る前に、「不良ゼロ」、「クレームゼロ」を実現し、「品質事故」の芽を摘み取りましょう。
プログラム
0.品質事故の実態
・品質事故の実態、品質事故の原因-1、2,3、4
・クレームの原因2007、クレームの原因2019、クレームをなくすには
1. マインドチェンジからモラルアップへ
・マインドチェンジ、トップの役割
・現場のモラルの崩壊、日本のモラルの実態
・モラルとは、モラルアップ
・品質セミナー、成果と効果
・マインドチェンジとモラルアップ、品質事故・クレームゼロの考え方
2. 検査作業改善へのアプローチ
・基本的な考え方
・クレームの原因、顧客条件による全数検査
・人の特性を活かしたST検査、検査者思いの改善
・情報のフィードバック
・人に頼った検査の限界、自動検査機の課題、AIにより自動検査、最後は人が保証する
・検査の目指す姿
3. 品質保証体制の整備
・品質保証体制の整備
・音声入力による報告書作成:改ざん防止
・スピード対応、火消し隊
・QTS
・早期情報公開
・品質部門の位置付け
4. 不良ゼロへのアプローチ
・不良ゼロの5原則:不良は結果、要因は71、対策は54、10のツール、要素別改善
・具体的な進め方、成功のポイント、健全なクレーム対策
5. ルールを守る人づくり
・なぜ守らないのか
・標準の実態、ない標準は作り、現在の標準は整備する
・従来の教育・訓練の欠陥、教育・訓練のしくみづくり、AIアドバーザー、計画的人材育成
・任せ切りの現場からの脱却
・ルールを守らないのは誰の責任か
6.設計ミスゼロへのアプローチ
7.部品不良ゼロ(購買)へのアプローチ
8.海外工場の品質マネジメント
講師紹介
1981年、ブリヂストンに入社。設備設計と保全業務に従事。1987年に日本DECに移籍し、
システム及びAIの開発に従事。
1992年、ロンド・アプリウェアサービスを設立。製造業を中心としたコンサルティングで
多くの成果を上げる。
不良ゼロを可能にする実践アプローチにもとづく指導方法に定評があり、国内メーカーに加え、
海外メーカーなどでも大きな改善効果を上げている。
また、ものづくりに特化したIoT/AIセミナーも数多く実施しており、改善とIoT/AIを
融合したこれからの時代の新手法を提案している。