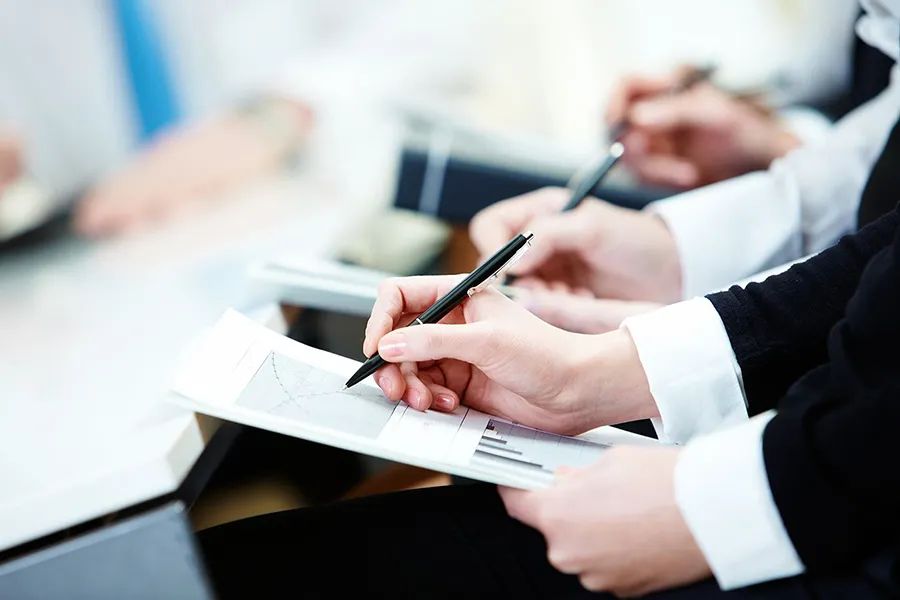
部品の仕様決め・検査プログラム,部品認定,長寿命設計,回路余裕度測定,製造ラインでかかるストレスの測定と制御,
製造現場の管理,変化に気づける人と職場風土等について解説する特別セミナー!!
- 講師
技術コンサルタント 伊藤 千秋 先生
オムロン株式会社 品質保証部長,部品技術部長等歴任後現職
制御機構部品の品質保証を15年,自動車電装部品の品質保証23年経験,品質・信頼性一筋のプロフェッショナル
この間,日本科学技術連盟 信頼性開発技術研究会 委員長などを歴任
- 日時
- 会場
- 受講料
- 1名:48,600円 同時複数人数申込みの場合 1名:43,200円
- テキスト
受講概要
受講対象
半導体をはじめとした電子部品のクレームやトラブルをゼロ化しようとしている企業の品質保証部門、設計部門、購買部門、 生産技術部門、設備部門、製造部門の技術者の方々
予備知識
特になし
習得知識
半導体をはじめとした電子部品の取り扱い技術、クレーム、トラブル時にメーカとの原因追求、再発防止歯止めを高める技術 1) 部品の仕様決めと検査プログラム,条件の検証 2) 部品認定の実力評価試験,構造解析 3) 長寿命設計と死にざま設計 4) 回路余裕度の測定と限界試験 5) 製造ライン・現場でかかるストレスの測定と制御 6) 製造現場の管理 7) 変化に気づける人の意識と職場風土の形成・しくみ
講師の言葉
半導体を主体とした電子部品のトラブルはその生産地が日本から海外、あるいはもともと海外だったものをふくめると 今では海外でつくられる電子部品が多くなり、ダイオード、トランジスタ、LEDや抵抗、コンデンサ、コイル部品などを 含めると今では日本国内で探すのすら難しくなってきた昨今である。 海外でつくられる部品が当たり前になり、それらが 増えてくることと合わせ、トラブルが起きた時の解析や真因追求の技術は下降の一途をたどっているといっても過言ではないだろう。 自社での技術や設備がないからその多くを電子部品メーカに頼らざるをえず、肝心なメーカに技術力の翳りが見えるとなると これは大変なことになる。「これは過電流破壊なので御社の使い方を見直し下さい」「これは偶発故障で実績ではXppmで 多発することはありません」といった「つきつけ型の回答」がいかに多いことか。技術力のあるメーカの探しだしや良質の材料、 設備、人材の確保されたラインを探し出すことは電子部品のクレーム、故障をゼロ化、極小化するにあたっての必須事項に なってきている。 昨今の半導体業界の勢力分布の変化やメーカ再編の動きは安全性・信頼性をより要求される部品や安さが売りの部品に大別され、 「車載用」「産業用」「民生用」などの業界用途別に分けられてこれに合わせた品質保証体制ができあがってきている。 車載用でいえば自動車機能安全規格ISO26262、車載用集積回路の故障メカニズムに基づいた信頼性試験AEC-Q100、 品質管理システムISO/TS16949などの要求規格が出来上がり、これらを取り込んだ半導体部品の品揃えも出来上がっている。 開発の効率化のためにこうした部品を友好的にとり込んでいくことが必要になってもいる。 その傍らで我々の回路設計は その部品の弱点を知らずして使い、皮肉にも弱点領域での使い方で品質トラブルを引き起こしたり、我々のライン、検査設備、 フィクスチャーでのアーク、ノイズ、サージを起こして電子部品にダメージを与え、故障の芽を仕込んでいることもしばしば あるのも事実である。 現場での作業者の意識が加工部品の%の管理に慣れきってしまっているところでは電子部品の故障は1個がロット不良のはしりで あることに気づかず、打ち手が遅れるマンネリ化しきってしまった職場が数多くある。 この講座はこうした半導体をはじめとした電子部品のトラブル、クレームゼロに向けての設計、購買、生産技術、製造、 品質保証の人々がなすべきこととその技術、しくみについて示すものである。
プログラム
(1) 半導体業界の信頼性の取り組み・体制の変遷 「車載用」「産業用」「民生用」などの業界・用途別の品質保証体制化の動き 自動車機能安全規格ISO26262と安全性・信頼性の高まりの関係 車載用集積回路の故障メカニズムに基づいた信頼性試験AEC-Q100との関係 品質管理システムISO/TS16949の定める先行製品品質計画APQP、製造部品承認プロセスPPAPとの関係 自社での半導体部品の評価・管理のありかた (2) 基本的な考え方 半導体における不良品、欠陥品、故障品とは 市場での故障ゼロを目指すには 海外部品調達から現地部品調達、現地生産、現地設計の種々なパターンにおける考え方 自動車電装部品の重要度区分とその品質保証体制の基本枠組み (3) 致命・重故障の品質展開と管理点の設定 故障モードの致命度評価 致命故障モードの故障の木解析とその展開の仕組み 車両評価、電装ユニット評価、部品評価、材料評価の組み合わせ品質保証体制 (4) 部品の仕様決めと検査プログラム、条件の検証 ベンダーパーツとサブコントラクトパーツの区分とその違い メーカならびに部品の認定の基本的な考え方 取引形態と契約の関係ならびにグローバル体制の中での契約書、仕様書のありかた (5) 部品認定のための実力評価試験、構造解析、ライン監査 デバイススペック・電装ユニットスペック・車両スペックの関係 電装ユニットの実力管理をするための構成部品の実力管理 認定分野とその区分と認定のプロセス 良い会社の見定め方15と良いラインの見定め方10 品質の顕在化、潜在化、底在化とそれらを引き出すためのやりかた 企業力評価とライン力評価の基本的な考え方とその例 実力評価試験と構造解析の基本的な考え方とその例 リニアIC、パワーMOS-FET、トランジスタ、LED、ダイオード、MPUなどの主要な故障事例とそこから得られる教訓15(ワイヤ接合欠陥、コンタクトホール欠陥、酸化膜欠陥、結晶欠陥、ステップカバレージ欠陥、過電圧破壊、過電流破壊、メタル欠陥、パッケージ欠陥) (6) 長寿命設計と死にざま設計 長寿命設計の押さえどころ 死にざま設計の押さえどころ マイコン暴走予防設計の押さえどころ 耐ノイズ設計押さえどころ 耐結露予防設計の押さえどころ 耐熱設計の押さえどころ 振動予防設計の押さえどころ (7) 回路余裕度測定と限界試験 特性保証・動作保証・故障モード保証とそれぞれの考え方 限界試験・複合試験・動作信頼性試験とそれぞれの考え方とやりかた 主要な特性の余裕度測定のしかた(電圧変動、電源瞬断、過入力、逆接続、サージ、チャタリング、応答性、CPU電源変動、振動子発振安定性、振動子起動安定性、VOL、VOH、IMax、 IMinなど) (8) 製造ライン・現場でかかるストレスの測定と制御方策 基板発熱温度分布の測定と正常品との比較による異常検知のしかた 基板ひずみ分布の測定と耐久限界を越えない工法の選びかた 操作振動並びに衝撃の周波数分布の測定と共振点を外す構造対策 電源ノーマルノイズ、コモンノイズ、誘導ノイズの立ち上がり波形・周波数の測定と対策 突入電流、遮断電流の立ち上がり波形・周波数の測定と対策 (9) ECUバーンインと即日解析体制 スクリーニング、デバッギング、エージング、バーンインの意味 欠陥を内在する部品を除く各種のやりかた 半導体の故障、スクリーニングに対するメーカ見解 市場実績から見た故障率の分布と除去が可能な故障モード、形状パラメータmの関係 効果的なストレススクリーニングの条件の決め方(電源、制御入力、負荷、温度、制御出力の動作シーケンスの組み合わせ) (10)インサーキットテスト、ファンクションテストなどのフィクスチャー、プローブピンをつかった検査設備の検証 インサーキットテスト方式、印加電圧、動作シーケンス プローブピンの種類、接触圧力、ストロークならびに寿命点、交換点 アークとノイズの関係ならびに最小アーク電圧と最小アーク電流の関係 ICT、FCTのプローブピン、フィクスチャーの検証の押さえどころ (11)静電気の測定・管理 帯電列 接触帯電、摩擦帯電、剥離帯電、流動帯電、噴出帯電、粉砕帯電 人体モデル、マシンモデル、デバイス帯電モデルとその試験法 ノイズ注入法、過電圧印加法のラッチアップ試験法 従来の静電気計測法と最新の静電気計測法 IECに定める絶縁抵抗測定・管理法 静電気の抑制と防止対策 (12)製造現場の管理 電子部品に損傷を与えないためのフローはんだ、リフローはんだの温度プロファイルの決めかた(表面実装、挿入実装、混載実装) 始業点検と就業点検とその間のセンシング、モニタ、警告・表示の方策 ポカヨケとその方策 異常管理とその方策 変化点管理とその方策 (13)変化に気づける人の意識と職場風土の形成、しくみ 作業ミスの背景を突き詰める4つの窓 変化に気づくことのできる現場の意識の醸成のしかた (14)実車試験 ワランティデータから故障モードを群分け ワランティデータからの故障の発生予測 故障車をつかまえて実車再現試験をするスクランブル体制 致命故障モード、多発故障モードのメカニズム解析と同一車種での実車再現試験による早期対処の体制